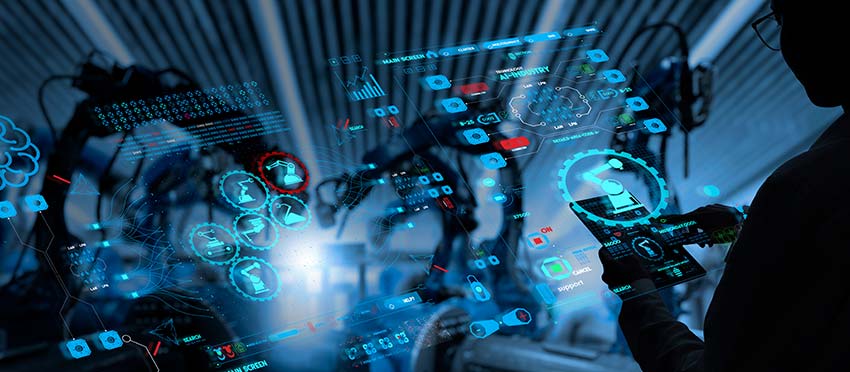
The fourth industrial revolution, otherwise known as Industry 4.0, is transforming the way businesses operate and is having a major impact on the global economy. With the introduction of new technologies, such as the internet of things, artificial intelligence, and robotics, companies are able to increase their efficiency, reduce costs, and improve customer service. However, many businesses are still struggling to capture the true value of Industry 4.0.
In order to capture the full potential of Industry 4.0, businesses need to focus on three key areas. First, they must invest in the right technology. This means investing in the latest technologies, such as the internet of things, artificial intelligence, and robotics, as well as ensuring their existing systems are up to date. Second, businesses need to invest in the right people. This means hiring the right talent and providing them with the necessary training and resources to be able to make the most of the new technologies. Finally, businesses need to invest in the right processes. This means creating processes that are automated and streamlined so that the new technologies can be used to their fullest potential.
By investing in the right technology, people, and processes, businesses can ensure that they are capturing the true value of Industry 4.0. This will enable them to increase their efficiency, reduce costs, and improve customer service. It will also help them to stay ahead of their competition and remain competitive in the global marketplace.
How To Adapt To Industry 4.0
Adapting to Industry 4.0, also known as the Fourth Industrial Revolution, involves a combination of technological, organizational, and cultural changes. Some steps that organizations can take to adapt to Industry 4.0 include:
Investing in digital technologies: Organizations should invest in technologies such as the Internet of Things (IoT), big data analytics, and artificial intelligence (AI) to improve their operations and gain a competitive edge.
Building a culture of innovation: Companies should foster a culture of experimentation and continuous learning to stay ahead of the curve in terms of new technologies and industry developments.
Developing new skills: As Industry 4.0 technologies become more prevalent, companies will need to develop new skills and capabilities to take advantage of them. This may involve training existing employees or hiring new talent with the necessary skills.
Reorganizing work processes: Industry 4.0 companies can help organizations streamline their work processes and improve efficiency. This may involve reorganizing teams, automating certain tasks, or redesigning entire business models.
Collaborating with partners: They often require collaboration between organizations, whether it’s to share data, develop new products or services, or create new business models.
Embracing security and privacy: As Industry 4.0 technologies are more connected, companies should be more aware of the security and privacy risks and implement the necessary security measures to protect their data and assets.
It’s important to note that Industry 4.0 is a rapidly evolving field and it’s important to stay up to date with the latest developments and trends to fully take advantage of the opportunities it presents.
Delivering Value Across Every Area of The Factory
This digital transformation is revolutionizing all aspects of manufacturing, from processes and productivity to people. By leveraging the right technology, manufacturers are able to make more informed decisions, create new opportunities for upskilling and reskilling, attract and retain better talent, and improve workplace safety and employee satisfaction.
It has a major impact on people. By leveraging digital technologies, manufacturers can create new opportunities for upskilling and reskilling their workforce. This allows them to remain competitive in the changing landscape of the manufacturing industry. Additionally, digital transformation can help manufacturers attract and retain better talent. By offering employees the opportunity to learn new skills and gain new experiences, manufacturers can create a more attractive workplace and retain top talent.
It can also help improve workplace safety and employee satisfaction. By leveraging digital technologies, manufacturers can monitor their operations in real time and quickly identify and address any potential safety issues. Additionally, digital transformation can help improve employee satisfaction by providing employees with access to better tools and resources.
You can contact iSIMPlatform at www.isimplatform.io or at info@isimplatform.io for solutions that make life easier and smarter.
No responses yet